The Harwyn Pod: a picture of the burgeoning Aussie prefab industry
- Nathan Johnson (originally published in
- Jun 25, 2015
- 2 min read
“Consider that 25 years ago, the closest thing we had to an iPhone isn’t really anything more than a museum piece, I think technologies that both exist and are about to come into existence are going to revolutionise the way we approach modular building over the next 25 years,” Jason Fremder, Managing Director, Harwyn.
Whether it’s the design and construction of buildings in offsite factories, or the more focussed manufacturing of modular units such as bathrooms and insulated panels, there is no denying that the prosperity and variety within the Australian prefabrication industry is growing exponentially each year.
One design and construction outfit well and truly “all-in” for the now $4.6 billion prefab industry is Harwyn, a small team in Victoria who factory design, build and detail a range of prefabricated office “pods” that they then deliver to site.
The Harwyn Pods are designed by the firm’s in-house architect Selwyn Blackstone and come in four sizes, ranging from the 2.2m x 2.2m ‘Mono’ pod, to the Harwyn ‘Super Maxi’ which is 3.15m x 5.3m.
Buyers can simply walk into the Harwyn showroom, point at the size, colours and furnishings they’d like for their pod and then expect it to arrive by truck and craned into their position of choice within five weeks.
Managing Director of Harwyn Jason Fremder notes that the speed and quality of his team’s pods has benefited from recent advancements in prefab materials and products.
“As far as Harwyn is concerned, we have been able to do away with traditional framing and apply an insulated sandwich panel, which we utilise for walls, floors and roofs,” he explains.
“The stiffness of the interlocking panel and spanning ability for floor and walls allows us to very quickly construct the Pod on a steel base prepared for cranage or fork lift, and ready for transport.”
He also notes that prefab manufacturing technology is improving and becoming more cost effective.
“We are [also] working with CNC machines that not so long ago were only accessible by very few,” says Fremder.
“Going forward, there will be many opportunities to utilise the many new technologies that are becoming more and more affordable.”

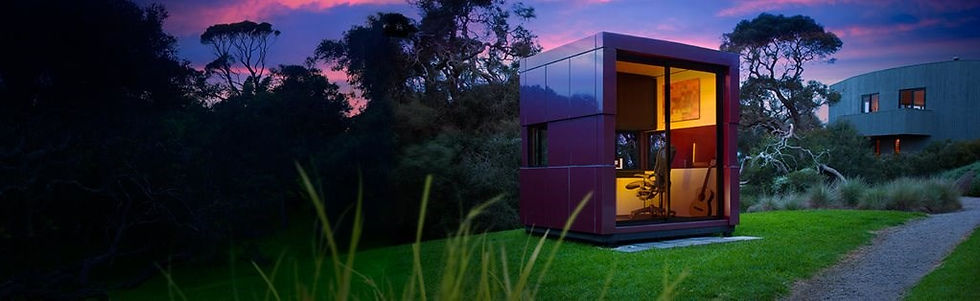
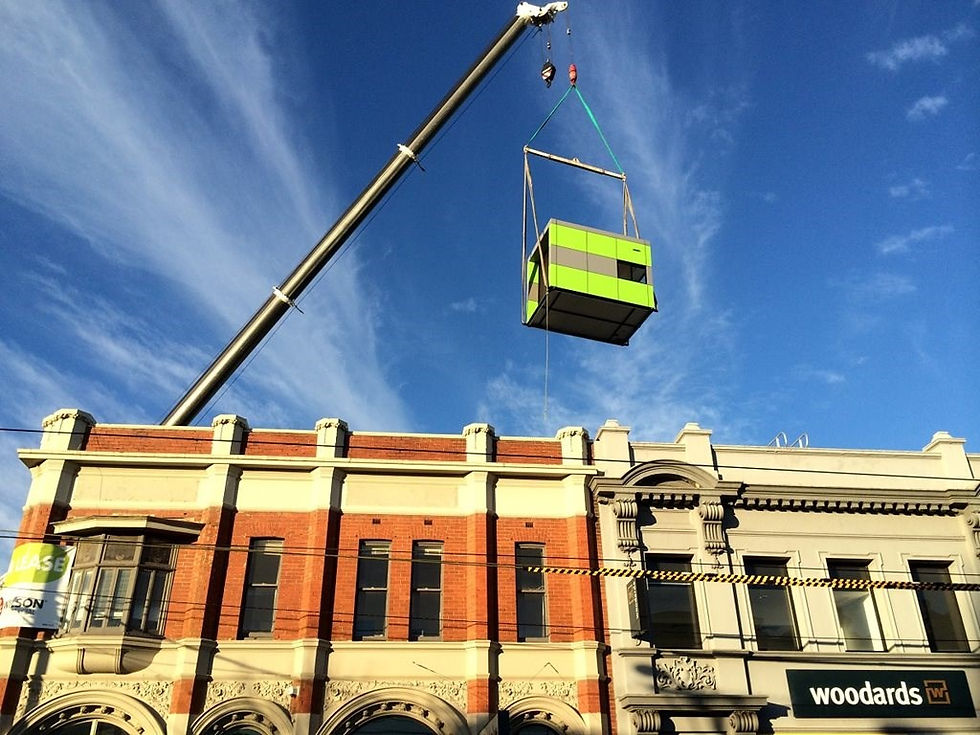


The pods are constructed with Kingspan PIR panels which interlock to provide a tightly sealed envelope, an insulation equivalent of 120mm of EPS foam, and also remove the need for structural framing and traditional foundations.
Alucobond ACM panels are used to clad the exterior of the pods to provide a decorative element (they come in a large range of colours and finishes) and an extra layer of insulation.
Window and door frames are from Taranto and Harwyn use Viridian EnergyTech™ ‘Grey’ glazing which has a pyrolytic low emissivity coating that is fused at extremely high temperature when the glass is being made to produce a durable hard transparent coating on one surface of the glass.
Beyond the basic size and structure, the Harwyn range can also be fitted out, for a cost, with all the bells and whistles seen in contemporary offices such as Tretford carpets, Sonos audio-visual products and Apple TV.
The Harwyn Pod was a recent winner of the 2015 Good Design Award for best in Commercial & Residential Architecture category.
View the original article: http://www.architectureanddesign.com.au/projects/large-commercial/the-harwyn-pod-a-picture-of-the-burgeoning-aussie
Comments