Sync Building Systems by Hickory - Tour with Chris Ong
- Dino Vrynios
- May 15, 2015
- 3 min read
I met with Chris Ong Commercial Director of Hickory’s Sync Building Systems at their Bathroom Pod manufacturing facility across the road from Modscape at Brooklyn.
After introductions, Chris signed me in, kitted me out with all the safety gear and we passed through the office into the facility beyond.
I have never seen anything quite like it. In front of me were rows and rows of Bathroom Pods at various stages of construction on the production line.
The whole process starts with Design & Planning by an Architect. The bathroom is designed to fit in with the layout of the building and as a rule the number of different bathroom types for anyone building is kept to a minimum to ensure maximum efficiency. A BIM 3D Model is produced as well as the shop drawings and bill of materials.

From there we move to the factory and Chris takes me to start of the product line, the patented Glass Reinforced Concrete (GRC) base. It is essentially a lightweight concrete slab that has been produced using a mould designed in the BIM 3D Model. The base removes the need for a recess to be built into the building slab and ensures the risk of leaks is mitigated as the entire bathroom walling is essentially on a 100mm hob. I quizzed Chris on the cost and time of R&D it took to develop the bathroom pods. What follows is a paraphrased account of what he said:
‘Hickory has been building apartment buildings for 20 plus years and basically we have learnt through that process the problems having bathrooms built in-situ present. They leak. We have one million dollars in our annual budget for maintenance on buildings.’
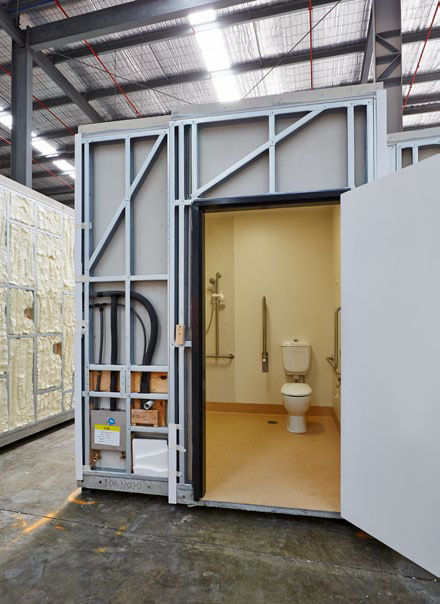
From there we move to the wall framing. In front of me are two ‘stations’. Working from left to right there is a roll of flat galvanised steel which then runs through a rolling machine connected to a computer. The computer has the BIM model in it and tells the rolling machine to roll and cut the exact lengths required with necessary pre-punched penetrations for plumbing and services. The rolled galvanised steel frame lengths are then assembled into the walls of the bathroom pod by four workers. The four walls are then put in place and the pod is ready for first fix services, lining, screeding, painting, tiling, joinery and finally second fix installation.

By the time we reach the end of the line an automated robot is wrapping the pods in protective plastic ready to be shipped off to its final destination. Each pod has a clipboard with a barcode that is used to tracks all information throughout its production. Chris says that at optimum performance they can produce 12 pods per day. They are currently operating at 10 per day after recently having a project with 40+ different bathroom layouts which slowed production.

On that particular project the Sync Building System came after the building design was finalised. Chris said they took the hit on that project because they knew it would lead to future work, at which time they can be involved much earlier in the design process.
Each pod costs approximately 11-12K and if you factor in all the other benefits like better delivery time, less waste, its fully recyclable and requires half the transport energy, the value is undeniable.

I asked Chris his thoughts on the future of their operation and its scalability. He said they are definitely growing and with their neighbours from the structural systems side of the factory moving out soon, they will have more space. They are currently providing pods for projects in Melbourne and along the east coast. Shipping internationally though has not been achieved as the height of the pods doesn’t work with containers.
On whether or not something like this would work in Adelaide, Chris believes that the demand may not exist. I tend to think he is right when looking around the number of apartment buildings going up around Melbourne (housing for an extra 100,000 people is required each year) compared to what is happening in SA.


Nevertheless, it is a great example where skilled workers from the automotive and components industries in South Australia could be re-employed in the construction industry.
*All images have been taken from the 'Sync Building Systems. Overview of Bathroom Pod Technology' brochure downloaded from the Hickory website.
Comments