Modscape Brooklyn Facility Visit
- Dino Vrynios
- May 14, 2015
- 3 min read
There are three things that greet you on your arrival at Modscape’s Brooklyn offices, sales centre and construction facility.
Firstly, the enormous corrugated clad construction facility which has existed for many years before Modscape ever did. This 6+ storey former foundry is visible well before you enter the car park. In this industrial area, the metal building is a visible landmark as you make your approach from the Melbourne CBD along the Princes Highway.
Second is a ‘display home’ with modernist lines and black timber cladding; a stark contrast from the white gravel that surrounds it.
Finally, slightly obscured behind the display home is a fabrication yard teeming with trades and multiple buildings and skeletal steel chassis’.

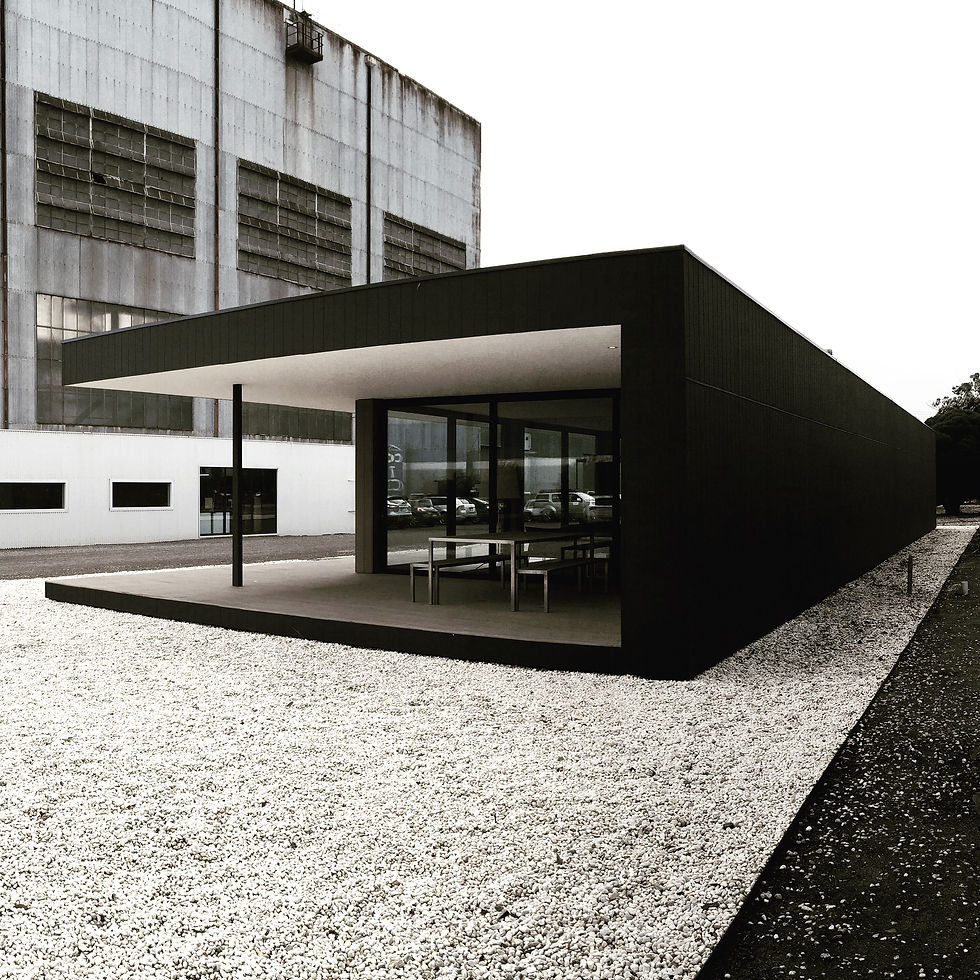

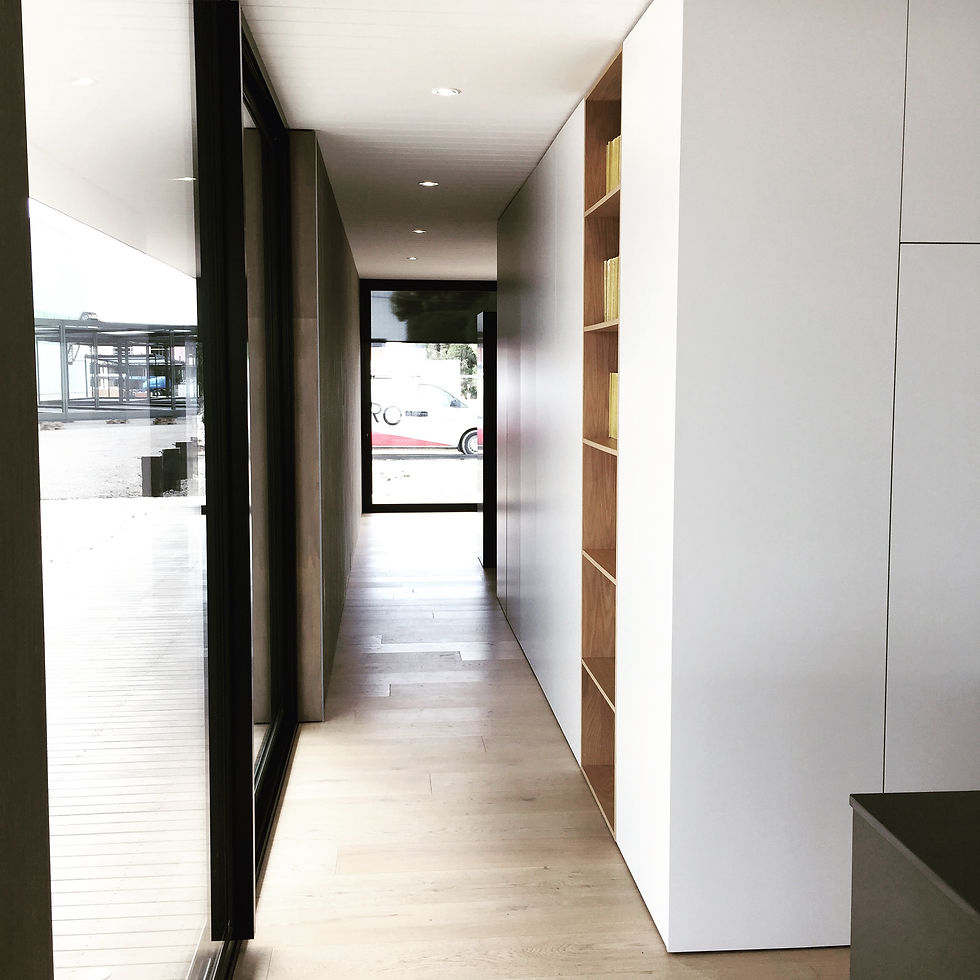

I venture inside the office; a modular addition to the original foundry beyond. I am greeted by Dawn Muir who heads up marketing and sales at Modscape, but also possesses an Architecture degree.
The following is a selection of key points from our wide ranging conversation.
Modscape was established 9 years ago by Jan Gyrn (and partners) specialising initially in modular residential.
Whilst they have always undertaken a mix of residential and commercial projects, 4 years ago they made a strategic decision to branch out into the helth sector with great success. Health and Eductaion proects now make up 60% of all work.
45 staff on their books at any one time (1 x Managing Director, 1 x Construction Manager, 1 x Design Manager, 1 x Factory Manager & Supervisor, 1 x Sales & Marketing Manager, 1 x Accounts & Admin, 1 x full-time Architect, 1 x part-time Architect, 4 x Draftspersons, 1 x Estimator, 2 x Contract Administrators with the rest being full time tradespeople.)
Modscape provide a ‘one stop shop’ turn-key solution.
Collaborate often with Architects who ask ‘how can we modulise this?’
Predominantly private and commercial clients – no government work
Ongoing issues with banks for finance with their clients as they have issues recognising/understanding the procurement process for prefabrication off site.
Also has taken time for insurers to understand the process.
The condensed time frame can have an impact with finances also as the release of funds is frequent and quite large comparative to traditional construction.
Have seen a shift away from ‘holiday home’ type remote residential projects to more ‘urban sites’ in the suburbs and CBD.
Provide private hospitals and mental health accommodation facilities which are completely fabricated and fitted out on site with external specialist trades utilised where required.
Having a team of in-house tradespeople is crucial to the operation of the business.
5 – 6 projects under construction at any one time.
About to complete a four storey residential project that will require a new crane to be installed in the facility. The building will be completely fabricated and assembled as the four storey building inside the facility before being transported to the site.
An extension to the existing facility is earmarked for the near future to accommodate their growth.
Three separate projects currently being built in the yard as there is not enough space inside the former foundry facility.
One of these is actually being placed on top of an existing 7 storey multi-residential building.
Predominantly fully welded steel frame chassis with steel wall framing.
Utilise Bondor Structural Insulated Panels (SIP’s) to the floor and wall which not only are made from recycled materials and are recyclable, but also help create extremely efficient buildability and provide excellent thermal performance.
I knew before I saw Modscape’s operation first hand that they were market leaders; however that did not stop me from being blown away by the buildings.
They have a very sophisticated model where every detail has been considered and refined over time.
Their marketing material is beautiful, their website is clear and simple, their staff are knowledgeable and passionate, but most importantly their product is as good as anything you might have built on site over 8 months.
Many thanks to Dawn for being such an obliging host and I look forward to speaking with Jan on Monday.
*I was unable to take photo’s inside the facility and of projects under construction due to confidentiality. I will be provided images later this week.*
Comentarios